Imagine standing on a drilling rig, the world whirling beneath you, as a powerful jet of oil and gas erupts from the wellbore, a colossal geyser of uncontrolled energy. This is a blowout, a catastrophic event that can cause devastating environmental damage, loss of human life, and massive financial repercussions. It’s a nightmare scenario that every drilling engineer strives to prevent.

Image: www.pdffiller.com
The key to averting these disasters lies in the discipline of well control, a multifaceted field dedicated to ensuring safe and efficient drilling operations. Well control procedures, equipment, and training are designed to anticipate potential problems and react decisively to any sign of hydrocarbon flow. But mastering well control requires a fundamental understanding of its principles and practices. This article will provide an in-depth look at well control, exploring its fundamental concepts, practical applications, and essential techniques. It will also guide you through common well control questions and answers, providing valuable insights for anyone involved in the oil and gas industry.
Understanding the Fundamentals of Well Control
At its core, well control is about managing the pressure of fluids inside a wellbore. Imagine the wellbore as a vertical pipeline, filled with drilling mud and potentially containing hydrocarbons under immense pressure. When these fluids encounter a sudden release, like a breach in the wellbore, they can surge upwards, causing a blowout.
Well control techniques aim to manage this pressure and prevent uncontrolled flows. By using specialized equipment, drilling fluids, and procedures, well control engineers can ensure the wellbore remains under control, minimizing the risk of a blowout.
Essential Well Control Equipment: Your Arsenal Against Blowouts
Effective well control relies on a range of specialized equipment designed to mitigate and control pressure surges. Here are some of the key components:
Blowout Preventer (BOP): The Last Line of Defense
The blowout preventer is the linchpin of well control, a massive assembly of valves and rams deployed at the top of the wellbore. When a blowout threatens, the BOP is activated, sealing off the wellbore and preventing further flow. There are two primary types of BOP’s:
- Annular BOP: This type uses a series of rams to seal the wellbore, effectively clamping down on the casing and tubing to prevent flow.
- Blind Shear BOP: This type utilizes blades to shear and seal the drill pipe, efficiently stopping flow when the annular BOP can’t isolate the well.
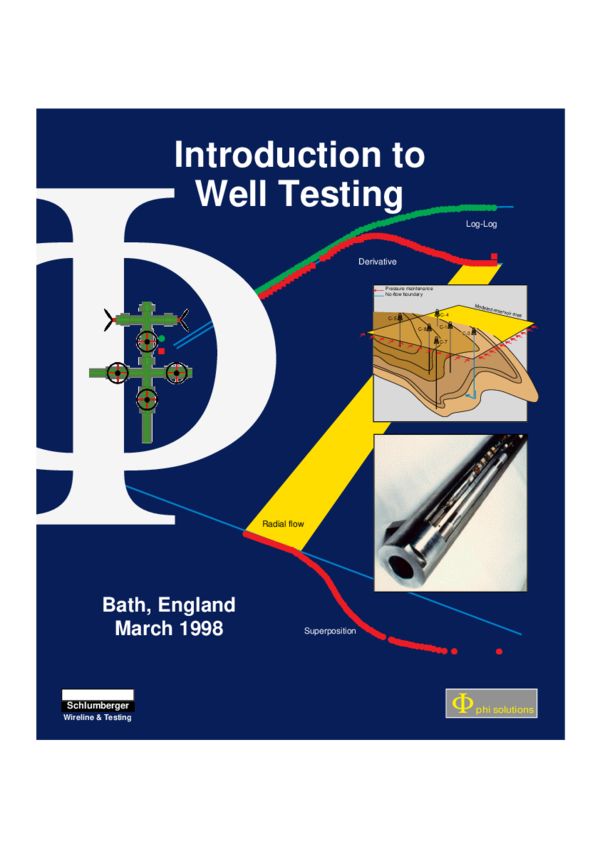
Image: www.academia.edu
Drilling Fluids: The Lifeblood of Well Control
Drilling fluids, also known as mud, play a crucial role in maintaining well control. They accomplish several vital functions:
- Pressure Control: Drilling mud exerts hydrostatic pressure on the wellbore, counteracting the pressure from underground formations and preventing uncontrolled flow.
- Hole Cleaning: Mud circulates through the wellbore, carrying drill cuttings and debris to the surface. This prevents the accumulation of cuttings, which can plug the wellbore and impede drilling progress.
- Stability: Drilling mud helps stabilize the wellbore walls, preventing them from collapsing or caving in.
Well Control Techniques: Handling Pressure with Precision
Well control techniques encompass a range of procedures and strategies used to manage pressure and address potential problems. Here are some key ones:
Drilling Fluid Weight: Striking the Right Balance
The weight of drilling mud is a critical factor in well control. By adjusting the mud weight, engineers can balance the hydrostatic pressure against the formation pressure, maintaining a stable and safe environment during drilling. Here are the general guidelines for mud weight adjustment:
- Overbalance: When the mud weight exceeds the formation pressure, it helps prevent flow from the formations into the wellbore. This is typically used when drilling through high-pressure formations.
- Underbalance: When the mud weight is lower than the formation pressure, it can lead to flow from formations into the wellbore. This technique is often employed when drilling through low-pressure formations or for stimulating production. However, underbalanced drilling requires careful monitoring and strict control to avoid uncontrolled flow.
Wellbore Circulation: Keeping Things Moving
Maintaining continuous circulation of drilling mud is vital for well control. Circulation helps remove drill cuttings, maintain pressure balance, and prevent formation fluid influx. When circulation is lost, it can indicate a wellbore problem and necessitate immediate action.
Real-World Examples: Lessons Learned from Blowouts
Well control incidents provide critical lessons for the oil and gas industry. Studying past blowouts highlights the consequences of procedural failures, equipment malfunctions, or unforeseen geological conditions. Here are some infamous examples:
The Ixtoc I Blowout (1979)
The Ixtoc I blowout in the Gulf of Mexico stands as a stark reminder of the environmental devastation a blowout can cause. It lasted for nearly 10 months, releasing millions of barrels of oil, impacting coastal ecosystems and marine life. The root cause was a combination of poor well design, a series of engineering errors, and a lack of adequate safety measures.
The Deepwater Horizon Disaster (2010)
The Deepwater Horizon disaster, with its massive oil spill in the Gulf of Mexico, is perhaps the most recent and widely publicized example of a blowout. The incident was triggered by a catastrophic failure in the wellbore, coupled with inadequate safety protocols and regulatory oversight. The disaster led to a significant overhaul of well control regulations and increased emphasis on safety measures in the industry.
Well Control Training: Equipping Workers for Safety
Well control training is an essential component of safe drilling operations. It ensures that personnel involved in drilling activities have the necessary knowledge and skills to recognize and respond to potential well control issues. Well control training programs cover a variety of topics, including:
- Fundamentals of well control: Basic principles, terminology, and concepts related to well control.
- Equipment operation: Familiarity with the use and maintenance of well control equipment, such as blowout preventers (BOPs) and other safety devices.
- Drilling fluid technology: Understanding the properties and functions of drilling fluids, including their role in well control.
- Emergency response procedures: Training on how to respond to a well control incident, including evacuation procedures, equipment activation, and communication protocols.
Well Control Questions and Answers: A Practical Guide
Here are some frequently asked questions about well control, along with answers to help you better understand the topic:
1. What are the key steps involved in well control procedures?
- Pre-drilling planning: Thoroughly evaluate wellbore conditions, potential hazards, and appropriate well control strategies.
- Drilling fluid optimization: Select and adjust drilling fluids based on formation conditions and desired pressure balance.
- Wellbore circulation: Maintain continuous circulation of drilling mud to remove cuttings and maintain pressure control.
- BOP and other equipment: Ensure proper operation and maintenance of well control equipment.
- Monitoring and communication: Continuously monitor wellbore conditions and communicate effectively between personnel.
- Emergency response: Be prepared to respond to well control incidents effectively.
2. How can a well control problem be identified?
Recognizing potential well control issues requires vigilance and keen observation. Here are some telltale signs:
- Loss of circulation: Difficulty in maintaining continuous circulation of drilling mud. This can indicate a leak in the wellbore or other problems.
- Pressure changes: Sudden increases or decreases in wellbore pressure, suggesting possible flow from the formation or other pressure anomalies.
- Gas kick: Gas entering the wellbore, indicating a potential for uncontrolled flow.
- Drilling fluid contamination: Changes in drilling fluid properties, potentially indicating a formation influx.
- Unusual wellbore behavior: Any deviation from normal drilling operations, requiring investigation.
3. How do you react to a well control incident?
Responding to a well control incident involves a series of coordinated actions to shut in the well and address the problem. The specific steps may vary depending on the severity and nature of the incident. Here’s an overview of the typical process:
- Identify the problem: Assess the nature of the incident and its potential consequences.
- Secure the wellbore: Close any open valves and activate necessary safety equipment, including the blowout preventer (BOP).
- Kill the well: Use appropriate well control techniques to stop any further flow of fluids into the wellbore. This typically involves increasing the pressure in the wellbore or using other methods to isolate the problem zone.
- Assess damage: Evaluate the extent of damage caused by the incident and determine necessary repair or remedial actions.
4. Why is adequate well control training essential?
Proper well control training is crucial for ensuring the safety of personnel, protecting the environment, and minimizing the risk of costly blowouts. It equips workers with the knowledge and skills to:
- Recognize potential hazards: Identify early warning signs of well control problems and effectively communicate them.
- Operate equipment safely: Understand the proper use and maintenance of well control equipment, including the blowout preventer (BOP), and follow safety procedures.
- Respond effectively to incidents: Implement appropriate well control procedures in case of a blowout, gas kick, or other wellbore emergency.
5. What are the latest trends and developments in well control technology?
The well control industry is continuously evolving with advancements in technology and best practices. Some recent developments include:
- Automated well control systems: Integrated systems that monitor well conditions and automatically activate safety measures if necessary, minimizing human error and enhancing response time.
- Advanced drilling fluid technology: Improved drilling fluids with enhanced performance characteristics, offering better pressure control, hole cleaning capabilities, and formation stability.
- Wellbore monitoring tools: Sophisticated tools that provide real-time data on wellbore conditions, allowing for proactive monitoring and early detection of potential problems.
Well Control Questions And Answers Pdf
Conclusion: Mastering Well Control for a Safer Future
Well control is a critical aspect of the oil and gas industry, safeguarding lives, mitigating environmental risks, and ensuring operational efficiency. This article explored the fundamentals of well control, essential equipment, key techniques, real-world examples, and practical questions and answers. By understanding these principles and best practices, we can work towards a safer and more sustainable future for the industry. As technology continues to advance and our knowledge grows, we must strive for continuous improvement in well control practices to prevent blowouts and safeguard our planet.